Sound Dampening is Nothing to Keep Quiet About
Builders of multifamily buildings, especially in the last few years, have a new catchphrase, “acoustic privacy,” and they are taking this term very seriously. A tenant’s noise complaints can possibly escalate to a point where they end up in front of a judge. As a result, more and more general contractors, architects, designers and engineers are putting acoustic privacy under the microscope from a construction project’s concept through its completion. In today’s highly competitive marketplace where buyers are more cautious than ever… and, an educated consumer is still the best customer, absolutely NOBODY wants to be disturbed by their neighbors!
Working on lavish multifamily high-rises, savvy designers seldom plan for gathering rooms that could emit loud noises to be positioned next to residential living units. In other words, they’re not going to put a fitness room adjacent to apartments. Clearly, tenants don’t want to hear cacophonous sounds coming from a large, early morning spinning class… or the pounding of feet from a spirited Zumba workout. Overall, the entire building team, from the developer on down, for the most part knows the vital importance of making sound decisions about sound management for their respective projects.
A good indication of what experts consider when planning how best to address sound issues, was discussed by Scott Banda, Bostik’s Director of Marketing & Business Development, who stated, “There are three basic types of noise transmission found in today’s multi-family residences. ‘Airborne,’ such as voices or music; ‘Impact,’ from footsteps or dropped objects… and, ‘Structural Component Movement’ (resulting in squeaking or creaking floors).
“Local building codes have standardized on two methods of measuring noise,” Banda continued. “STC (Sound Transmission Coefficient) measures the airborne sound moving through a floor, and IIC (Impact Isolation Class) measures sound from impact on the floor. Both can be measured in a laboratory as well as on-site. The International Building Code (IBC) requires a lab IIC of 50 dB (45 dB field measurements) and a lab STC of 50 dB (45 dB field measurements). In both cases, the higher the number, the better the performance of the sound abatement material. While not all local building codes are the same, the UBC is the most common benchmark in the U.S.”
Today, most developers, GC’s, their subs and suppliers are on the same page relative to soundproofing in construction, which can be defined as “a combination of many different means to achieve the goal of reducing sound pressure with respect to a specified sound source and receptor.” Or in layman terms, simply “to reduce the sound one hears.”
In America, especially in higher-end residences, natural hardwood flooring continues to be in demand. Wood flooring has many advantages over other types of flooring. It adds value, warmth and style to both new and newly renovated homes. Installation generally will cost more than purchasing new carpet. However, premium wood floors can last more than 100 years with regular maintenance and minor repair. The majestic “look” of wood combined with the fact that it is a green, sustainable product of Mother Nature, makes it an even more attractive surfacing decision. And, because it doesn’t harbor allergens or dirt, as do carpets and rugs, natural wood flooring continues to be highly desirable and sought after.
If wood flooring does have an ostensible downside or two, these most likely will have to do with sound. In particular, with “impact” such has the reverberations from footsteps or dropped items… and with ‘structural component movement.” (We’ve all walked on a creaky wood floor at one time or another.)
“Right now,” added Banda, “adhesive acoustic membranes are emerging as the fastest-growing segment of the sound abatement systems market, especially in specifications for high-rise, residential construction. Other, more established products can be used in conjunction with high-performance adhesive membranes to further increase sound dampening, moving from a solution that simply passes code … to a system that dramatically increases the comfort of the space and virtually eliminates one of the most common complaints of multi-family living.”
To meet or exceed building code requirements… up until now architects and designers generally have specified cork, rubber or composite underlayments to function as sound abatement barriers relative to airborne or impact noise transmission. With these newer acoustic solutions, new developments in adhesives have surfaced.
Strategically specified sound solutions can actually have positive effects on the project’s timeline. For example, advanced hardwood flooring adhesives that include sound abatement within their respective formulations can be installed in the same time required to install a glue-down hardwood floor. The installation of cork, rubber or composite membranes often requires the membrane to be glued down first, requiring a full day to cure before crews can come back to finish the hardwood installation.
Architects and designers must make sure that if a separate membrane is used for acoustic purposes, the increased height of the floor will not cause any problems. For example, using 1/4-in. cork is effective to achieve building requirements, but this installation increases the height of the floor by 1/4 of an inch… and, requires two layers of adhesive. Built-in cabinets, base molding and other items may need to be modified, sometimes by another tradesperson (such as a carpenter), to accommodate the increased height, increasing the cost of the project. Proper adhesive systems can typically eliminate the 1/4-in. thickness of the underlayment, and generally only result in the thickness of two credit cards.
Regarding floating floors, architects and designers should consider the acoustics within the room and extra expansion or contraction requirements. Floating floors can result in meeting IIC and STC values, but do not significantly reduce the sound of footsteps within the room. When there is an impact on a floating hardwood floor, the boards vibrate and thus, downward motion is absorbed. However, the upward rebound is not absorbed, resulting in a hollow sound in the flooring. Proper adhesives can reduce the vibration of these boards in both directions, resulting in a quieter floor.
Expansion and contraction of floating floors is also a concern. Bostik’s adhesives have elastomeric characteristics that create an anti-fracture membrane. That membrane bridges cracks up to 1/8 inch thick, that can occur in the substrate prior to… or after, installation. Elastomeric properties also allow the adhesive to move with the wood as it expands or contracts due to changes in humidity and temperature… throughout the entire life of the floor.
There is a belief that typical adhesive solutions are dependent on the skill of the contractor to establish and maintain the correct membrane thickness; that they are more susceptible to performance impact from inconsistencies in the substrate or flooring materials. To address this, Bostik’s Ultra-Set® SingleStep2™ was formulated with recycled rubber crumb spacers within the adhesive itself, to increase sound abatement performance and ensure the specified membrane thickness is consistent in size throughout the entire installation.
Using the right system of sound abatement solutions can increase the overall comfort of residents… and, virtually eliminate complaints about noisy neighbors (the bane of multifamily living!) For architects and designers, these
advanced adhesive membranes play a vital role in developing the best sound abatement systems for owners and developers of high-rise residential buildings.
Ultra-Set® SingleStep2™ provides Bostik’s highest level of acoustic performance. The adhesive contains Bostik’s patented AXIOS™ Tri-Linking™ Polymer Technology, offering polymer molecules that interweave themselves into a tight mesh, subsequently absorbing both impact and airborne sound waves. Ultra-Set® SingleStep2™ also contains 1 percent recycled rubber material; emits zero VOCs (as calculated per SCAQMD Rule 1168), and no water. And of course, with this product, there is no need for a separate acoustic membrane to be installed.
“All-in-one adhesives like Bostik’s Ultra-Set® SingleStep2™,” concluded Banda, “are amazing, time-saving installation systems that in addition to their acoustic control properties, also offer a lifetime warranty for unlimited moisture vapor protection with no concrete moisture testing required. We believe that if end-users are investing in beautiful natural wood flooring, it should be installed using the optimal adhesive system. One that actually helps keep neighbors neighborly.”
Let’s now talk about sound dampening regarding WALLS in a commercial project. Keeping noise blocked from one side of the building to another can be a challenging task, and again, may call for the expert input of an acoustical engineer.
Here’s an example: Imagine a large furniture retailer that sells its products out of a beautiful showroom. And, all or most of the products are inventoried within the attached, huge warehouse, right behind it. These SKU’s are methodically stocked in a gargantuan shelving grid from floor to ceiling. In that warehouse, there are loudspeakers, forklifts, trucks coming into the loading docks and other sources of discordant “sounds” that needn’t be heard in any showroom. Because of the new and technologically-advanced porcelain products specifically crafted to optimize wall coverings in commercial settings… there are also new adhesive systems that not only have been created for perfect, time-saving and long-lasting installations. These systems also have been formulated to offer high-performance sound dampening properties.
Meet Bosti-Set™, Bostik's latest advancement in adhesive technology. According to Adam Abell, Bostik’s Market Manager, Tile & Stone Installation Systems, “Bosti-Set™ has been painstakingly created to offer peak performance for thin gauged porcelain panels. One component Bosti-Set™ is an easy-to-trowel adhesive that revolutionizes how the design-build community works with thin gauged porcelain tile panels. It provides remarkable instant grab and holding power in a single coat application. Installers don’t need to back-butter both the panel and also apply the adhesive to the wall. Just one coat on one surface is all that is needed.”
“Bosti-Set™ provides non-sag, instant grab of thin gauged porcelain tile panels in sizes as large as 1/4" x 5' x 10' (6mm x 1.5m x3m). Installers need only to trowel on the back of the panel, eliminating the troweling of mortar on walls. Therefore, installation time reduced by as much as 50%, with half of the crew typically needed for typical mortar installations. There is also no need for mixing, water, and electricity to install the panels,” Abell continued. “Increased time-savings!”
Bosti-Set™ provides the ability to position panels up to 30 minutes while still preventing sagging. With 2% recycled material, 0% solvents, and zero VOC’s (Volatile Organic Compounds - as calculated per SCAQMD Rule 1168), Bosti-Set™ contributes toward LEED® credits under sections NC-v4 MR4.2: Recycled Content and NC-v4 EQ4.1: Low-Emitting Materials – Adhesives & Sealants
“But there is so much more,” exclaimed Abell. “Not only does Bosti-Set weigh up to 80% less than traditional mortar installations. It also guarantees exceptional acoustic performance for the long-term durability of the wall system.”
Figure 1, exhibits ASTM E 90 test results regarding the exceptional sound abatement properties of Bosti-Set™, comparing a standard wall to 3.5mm porcelain tile panels installed with traditional mortars and those installed with Bosti-Set™.
Why should salespeople working hard to make their commissions within their showroom environment have their efforts constantly interrupted by dissonant noise emitted from the warehouse?” Abell asked.
Scott Banda summed it all up by stating, “The only noises we want to hear are exclamations of specifiers, building owners and end-users who are acknowledging that adhesive systems for both horizontal and vertical surfaces… now have the wherewithal to offer world- class sound dampening performance!”
![]() |
Related News
Saturday, July 5, 2025

Bostik, a world-class leader in specialty adhesives and flooring installation systems, proudly announces the launch of Bostik Academy for North American contractors, distributors, and...read more
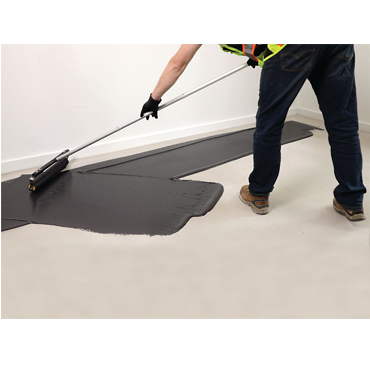
Bostik, Inc., a world leader in specialty adhesives and installation systems for building construction, has introduced Roll-Cote™, a high-performance moisture vapor barrier coating and primer, to the...read more

Wauwatosa, WI. July 30, 2021 ~ Bostik, Inc., a world leader in specialty adhesives and installation systems for building construction, has announced, beginning in August 2021, the rebranding and expanding of its soft floor covering installation systems...read more
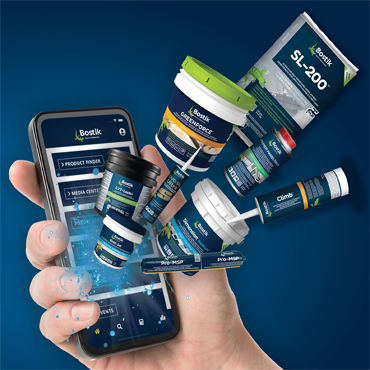
Bostik, Inc., a world leader in specialty adhesives and installation systems for building construction, has announced the release of its new App, the Bostik Pro™, available for free on both iOS and Android platforms...read more
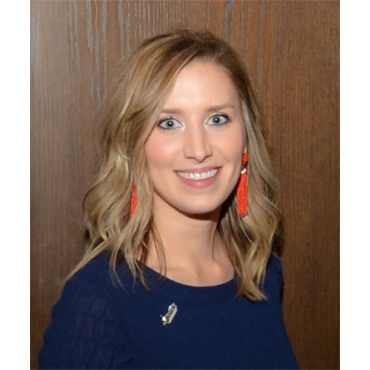
Wauwatosa, WI. March 23, 2021 Bostik, Inc., a world leader in specialty adhesives and installation systems for building construction, has announced several promotions and one appointment within its Consumer & Construction Business Unit, to support its current business plan for...read more
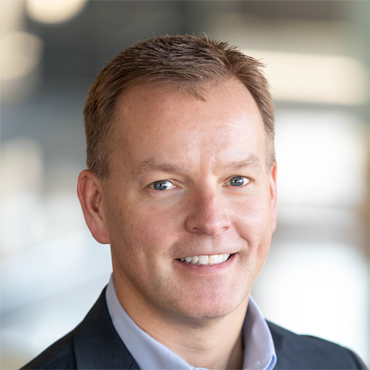
Wauwatosa, September 29, 2020 - Bostik, Inc., a world leader in specialty adhesives and installation systems for building construction, recently announced that Eric Loferski has joined the company as Director of...read more